How to Clamp Your Workpiece in a Mill Drill Machine
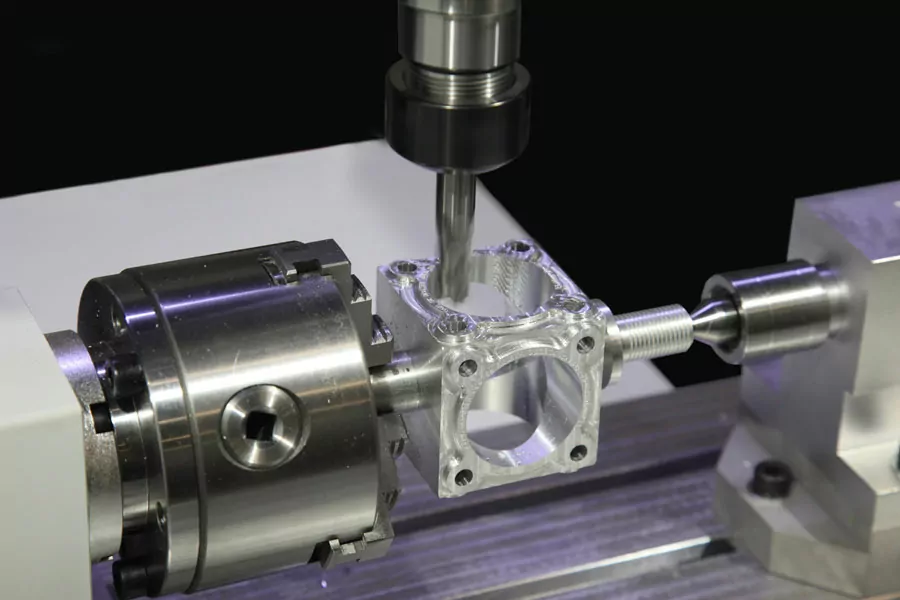
When securing a workpiece for precision milling, the right clamping technique is crucial. A mill drill machine requires stability to ensure accuracy during operations. The TE-CO Clamping Kit offers a comprehensive solution, providing you with various components designed to meet diverse fixturing needs.
With this kit, you gain flexibility and reliability, whether dealing with irregular shapes or standard materials—ensuring your projects maintain high standards of quality without compromising on efficiency.
Selecting the Right TE-CO Clamps
When you clamp, pick the right T-slot nuts. They fit with studs or bolts of many lengths. Combine these with clamps and step blocks to match your workpiece height perfectly.
Remember, a standard block is 25 mm thick; adding a large washer underneath ensures it won’t shift over the slot beneath. Now picture this: You set up steel tubing as risers for precision in height control, which is critical when milling heavy pieces that can’t afford any slip-up! This way, those sturdy tubes directly impact rigidity. Larger ones mean less wobble during cuts.
Bolt down several TE-CO clamps straight onto your machine table using threaded rods suited for the task at hand fast and firm, fixing made simple. Need stability on repeat jobs? Use a TE-CO clamp’s nose as an immovable stop by snugging it tight against each piece after placement!
So whether shaping single parts or batches, having a versatile TE-CO clamping kit ready could be what stands between success and second-rate results.
Positioning Your Workpiece Securely
To secure your workpiece, think about what holds it. Use jaw chucks for big or unequal pieces; their jaws grasp the outer shape firmly. For smaller parts, best under 3 inches, consider collet chucks’ accuracy and speed advantages.
They hug tight with a collar grip but won’t fit all sizes like jaw variants do. Your machine may have pallets to hold many items at once, slashing handling time. A tailstock supports one end while turning in machines that don’t move it themselves.
For precision jobs where every bit counts, remember: collet chucks beat standard boring-jaw chuck models on tolerance. They’re five times more accurate! Plus, they switch out fast, saving precious ticks when doing lots of small tasks or swapping between larger loads less often.
Adjusting Clamp Pressure Evenly
Ensure your workpiece sits tight in a mill drill machine. Set it up evenly with TE-CO clamping kits—drill without harming the table by using T-grooves for guidance.
For big holes, use parallel pads under your piece to protect the surface of our mill. When working on rectangles, secure them with a four-claw chuck and rotate for each new hole drilled. Always check that any V-blocks used are even in height; this is critical when drilling shafts or longer items.
Use flat-jaw vises for small pieces, but always ensure those pads have matching heights, too! Remember, step-by-step tightening prevents slips during intense milling jobs. Avoid uneven pressure at all costs.
Securing your workpiece correctly in a mill drill machine is crucial for precision and safety. Use clamps to ensure stability during operation. Always select the right clamp size, align it accurately with your material, and tighten it firmly without over-torquing.
Proper setup prevents slippage or damage, providing optimal results every time you tackle a milling project. Remember, effective clamping equals consistent machining excellence – so choose wisely!